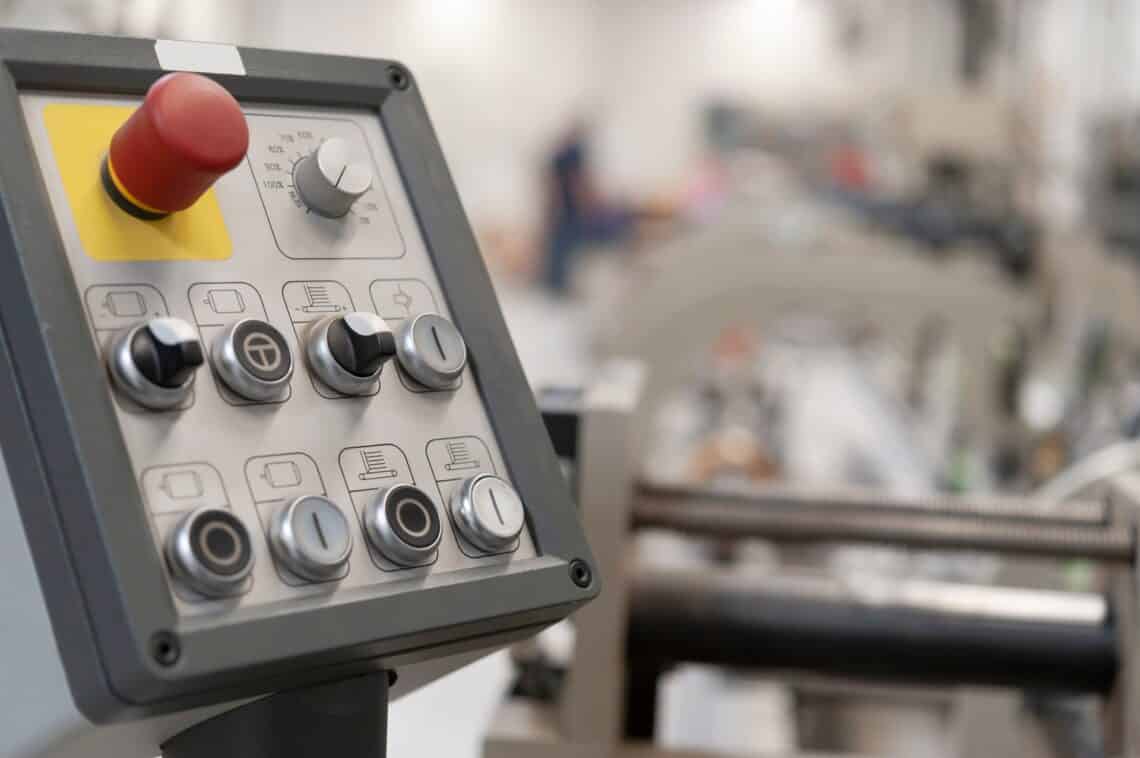
Was Stillstände im Betrieb wirklich kosten – und wie sie vermeidbar sind
Maschinenstillstände gehören zu den teuersten Risiken in der Industrie – häufig unterschätzt, selten geplant, oft fatal. Produktionslinien stehen, Liefertermine geraten in Verzug, Kunden beschweren sich. Die Kosten steigen in Minutenhöhe, während die Ursachen oft banal wirken: Ein fehlendes Bauteil, ein defekter Sensor, eine verspätete Lieferung. Doch gerade in einem eng getakteten Fertigungsumfeld genügt eine kleine Störung, um ganze Prozesse ins Wanken zu bringen. Oft fehlt ein zentraler Überblick über kritische Teile oder deren Verfügbarkeiten. Manuelle Prozesse, veraltete Listen oder nicht gepflegte Lagerdaten verlängern die Reaktionszeit. Techniker warten auf Material, während Maschinen ungenutzt bleiben. Der wirtschaftliche Schaden ist hoch – und wächst mit jeder Stunde. Wer Stillstände vermeiden will, muss nicht nur reagieren, sondern vorhersehen. Transparenz und klare Prozesse sind der Schlüssel.
Warum Reaktionszeit nicht reicht
In vielen Betrieben liegt der Fokus noch immer auf schnellen Reaktionen statt auf präventivem Handeln. Die Instandhaltung wird zur Feuerwehr, statt strategisch zu arbeiten. Ersatzteile werden ad hoc bestellt, Suchzeiten verlängern sich, Zuständigkeiten bleiben unklar. Gleichzeitig entstehen parallel unnötige Kosten für Notbeschaffung, Expresslieferung oder Leerlaufzeiten von Personal und Maschinen. Dabei wäre vieles vermeidbar, wenn Systeme konsequent miteinander kommunizieren und klare Prozesse hinterlegt sind. Eine vernetzte Datenbasis ermöglicht es, kritische Bauteile zu identifizieren, Wiederbeschaffungszeiten zu überwachen und Wartungszyklen präzise zu planen. Je besser die Vorarbeit, desto kürzer die Ausfallzeit – oder sie tritt erst gar nicht auf. Der Wandel vom Reagieren zum Steuern beginnt mit Transparenz und Struktur.
Wo SAP Ersatzteilmanagement ansetzt
Ein zentrales Werkzeug für den Umgang mit Ersatzteilen ist das SAP Ersatzteilmanagement, das die gesamte Kette vom Lager bis zur Instandhaltung digital abbildet. Damit lassen sich Bestände überwachen, Bedarfe automatisch erkennen und Teile intelligent priorisieren. Besonders bei komplexen Anlagen mit vielen Komponenten spielt die systemgestützte Koordination ihre Stärke aus. Das System verknüpft technische Informationen mit Lieferdaten, Wartungsplänen und Kostenstellen. Dadurch entsteht ein Überblick, der Entscheidungen fundiert und effizient macht. Kritische Teile können als „besonders relevant“ markiert werden, Mindestbestände definieren automatisch den Wiederbeschaffungszeitpunkt. So wird verhindert, dass ein einfaches Teil eine ganze Produktion lahmlegt. SAP ersetzt kein Personal – es entlastet es durch Struktur.
Das große Rechenbeispiel: Was Stillstand kostet
Die wirtschaftlichen Folgen eines Maschinenstillstands sind konkret messbar. Neben den reinen Produktionsausfällen fallen oft Zusatzkosten für Überstunden, Eilversand und verlängerte Rüstzeiten an. Bei einem Stundenumsatz von 10.000 Euro können wenige Stunden Ausfall bereits ein Projekt wirtschaftlich gefährden. Rechnet man Folgeeffekte wie Lieferverzögerungen oder Vertragsstrafen mit ein, steigt der Betrag deutlich. Je nach Branche summieren sich Stillstände zu sechsstelligen Jahresbeträgen – auch in mittelständischen Betrieben. Die genaue Höhe hängt vom Automatisierungsgrad, der Vorlaufzeit zur Behebung und der Verfügbarkeit von Ersatzteilen ab. Dabei ließe sich durch klare Planung und Datenverfügbarkeit vieles verhindern. Wer nur reagiert, verliert Zeit und Kapital. Wer strukturiert plant, verschiebt die Kosten von Ausfall zu Effizienz.
Checkliste: Frühwarnzeichen für vermeidbare Stillstände
Bereich | Typisches Risiko |
---|---|
Lagerhaltung | Fehlende Mindestbestände oder unklare Lagerorte |
Kommunikation | Keine zentrale Schnittstelle zwischen Instandhaltung und Einkauf |
Systembrüche | Daten in separaten Tools, keine automatische Synchronisation |
Lieferkette | Lange Wiederbeschaffungszeiten ohne Ersatzstrategie |
Schulung | Fehlendes Wissen über kritische Bauteile im Team |
Dokumentation | Veraltete Stücklisten oder fehlende Teilezuordnungen |
Verantwortung | Unklare Zuständigkeit bei Beschaffung und Bevorratung |
Priorisierung | Kein Überblick über besonders ausfallkritische Komponenten |
Interview: „Stillstand ist heute kein technisches, sondern ein strukturelles Problem“
Nico Bergmann ist Leiter Technische Services bei einem Automobilzulieferer mit rund 800 Maschinen im Drei-Schicht-Betrieb.
Wie häufig treten bei euch ungeplante Stillstände auf?
„Im Schnitt ein bis zwei pro Woche – manchmal nur Minuten, manchmal mehrere Stunden. Meistens wegen fehlender Informationen oder Teile, nicht wegen technischer Fehler.“
Was ist die größte Herausforderung bei der Vermeidung solcher Ausfälle?
„Die Datenlage. Wer was bestellt hat, wo ein Teil liegt, wie lange es dauert – oft sind die Informationen verstreut. Das kostet Zeit, Nerven und Geld.“
Welche Rolle spielen strukturierte Systeme bei der Lösung?
„Eine zentrale. Wenn wir alles in einem System sehen, reduziert das Suchzeit und Fehlentscheidungen. Der Unterschied ist enorm – vom Gefühl zur Klarheit.“
Gab es Widerstand gegen mehr Digitalisierung?
„Anfangs schon. Viele dachten, das sei nur Kontrolle von oben. Heute sehen die meisten: Es macht ihren Alltag einfacher.“
Was hat sich nach der Einführung eines PIM-gestützten Ersatzteilmanagements verändert?
„Wir haben mehr Ruhe im Prozess. Es gibt weniger Ad-hoc-Beschaffungen und mehr planbare Wartungsfenster. Die Teams arbeiten koordinierter.“
Welche Kennzahl hat sich für euch besonders verbessert?
„Die Reaktionszeit bei Störungen ist um 40 % gesunken. Und der Bestand an kritischen Teilen ist heute immer auf grün.“
Welche Empfehlung würdest du anderen Betrieben geben?
„Nicht warten, bis es brennt. Systeme und Prozesse gehören gemeinsam gedacht – das spart langfristig mehr, als es kostet.“
Wie geht ihr mit Lieferengpässen um?
„Wir pflegen Alternativen im System und planen Mindestmengen dynamisch. Das macht uns flexibler – gerade in Zeiten globaler Unsicherheiten.“
Kontrolle statt Krisenmodus
Stillstände kosten – Zeit, Geld und oft auch Vertrauen. Doch sie sind kein Naturgesetz, sondern die Folge fehlender Daten, unklarer Prozesse oder unzureichender Planung. Wer Transparenz schafft, kann reagieren, bevor es kritisch wird. Verschiedene Systeme helfen dabei, indem sie Abläufe strukturieren und Entscheidungen mit belastbaren Informationen unterstützen. Entscheidend ist jedoch nicht das Tool allein, sondern die Bereitschaft, Verantwortung neu zu denken. Wer Instandhaltung nicht als Reparatur begreift, sondern als Steuerungseinheit, senkt Risiken und schafft Sicherheit.
Bildnachweise:
Eigens – stock.adobe.com
Andreas P – stock.adobe.com
redaktion93 – stock.adobe.com
Das könnte dich auch interessieren
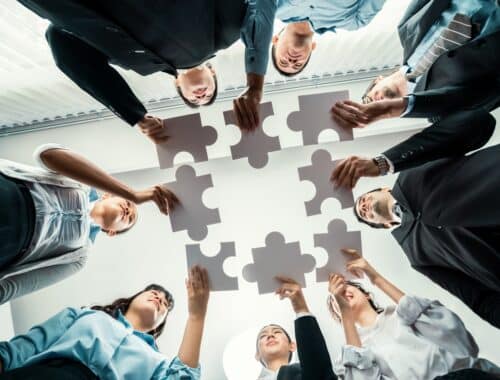
Effizienz als neues Geschäftsmodell: Was Unternehmen neu denken müssen
Juni 10, 2025
Industriehallen neu denken: vom Chaos zur Klarheit
Juni 9, 2025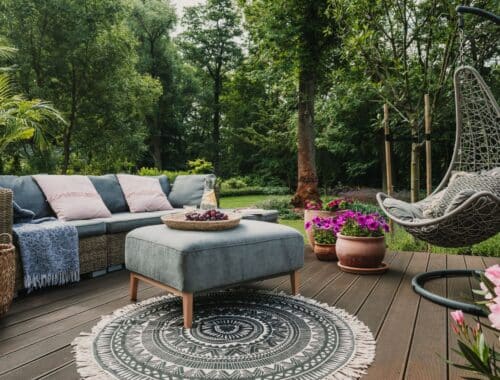